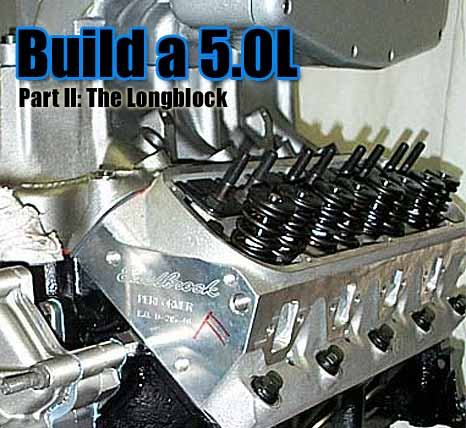 |
In the first part of this series we discussed the shortblock
build up. As mentioned, after some serious thought, we
decided to have the short block assembled by a local engine
rebuild and exchange outfit. We specified a stock 5.0L
shortblock, but paid a little extra to have the block
zero-decked in order to get compression to 9.5:1
We also upgraded to moly rings rather than the typical
cast iron pieces. (Moly-coated rings offer less friction
and thus increase power and reduce wear on the cylinder.
Cast iron rings seal faster and are more tolerant to imperfect
bore finishes. The choice is yours, but if you plan to
run the engine at the track occasionally, and rev beyond
5000 frequently, then the moly rings are a worthwhile
upgrade. By the way, these are standard gapped rings,
we don't see any major benefit to the "zero gap" style
rings on the market. It really depends on the builder
and their preference and recommendation.)
Before we even had the shortblock built we spent a good
deal of time evaluating the induction package that would
best suit our goal of power, economy and reliability.
With all of the choices out there, the decision was a
tough one.
We wanted a head and intake combination that matched up
well, and that would bolt on without the need for major
modifications, such pushrod length changes, new headers
or valve covers, etc.
We ultimately decided on Edelbrock heads and intake mainly
because it is a "tried and true" combination.
Their 5.0L heads have been around for many years, and
basically set the precedent for 5.0L aftermarket aluminum
heads. The quality and durability of the heads is close
to stock, in that this is a truly a bolt-on head that
can be expected to live for 100,000 miles without needing
new guides or other hardware. This is not to say they
are the best "flowing" heads on the market,
and in fact they fared in the middle of the pack in terms
of flow in our Head
to Head article.
Edelbrock offers three EFI intakes for the 5.0L engine.
The Performer, Performer RPM, and the Victor Jr. The Victor
Jr is for heavy breathing engines running in the 7000+
rpm range. An easy one for us to exclude.
Thus the choice came down to the Performer or the RPM.
Edelbrock advertises the RPM as having a powerband to
6500 rpm, while the standard Performer is listed to 6000.
(The difference is the RPM has slightly shorter and larger
upper intake runners, both intakes use the same lower.)
Not much of a difference, and our experience with the
same two intakes on the carbed side of Edelbrocks catalog
has shown the RPM to be a hands down winner , even for
engines operating well below 6500 rpm.
So we used that same reasoning here... why not get the
RPM to begin with and have a little better upper end power.
The cost might be some low end torque loss but even the
tech at Edelbrock assured us that is would be minimal.
We'll get back to you with our impressions once we have
some seat time.
We selected the Edelbrock Performer heads, part number
6037. This is their stud-mount head with a 60cc chamber
and 1.90" intake/1.60" exhaust valves. We opted
for stud mount due to the strength and adjustability of
studs and stud mount rockers compared to the stock pedestal
design. The 60cc chamber, with our zero-deck flattop piston
will yield an street ideal compression ratio of 9.5:1.
These heads also come with air injection ports for 50
state emissions compliance.
In terms of flow, our flow results showed a peak of 214
cfm @ .500" intake valve lift, and 172 cfm @ .500"
exhaust valve lift.
Some of you who have been following the chronicles of
our '88 LX may be asking why we didn't simply reuse the
Holley Systemax heads and Explorer intake combination
that was on this motor before the rebuild (see "Lung
Transplant" article in the archives.) This brings
us to the reason why we started this project in the first
place!
Holley heads and oil consumption
The Systemax heads we installed back in January (along
with an Explorer intake) ran very well out of the box,
powering our then AOD '88 LX to a 13.4 @ 102 on puny radials.
That was with no other induction changes -stock cam, throttle
body and mass air meter. However soon thereafter our motor
started consuming oil at the rapid rate. We knew immediately
that the problem was with the valve guides in the Systemax
heads.
As with Trickflow heads, Holley heads feature valves that
are rotated in the chamber to bring them closer to the
centerline of the cylinder. (Holley Systemax heads have
17 degree valve angles, stock heads are 20
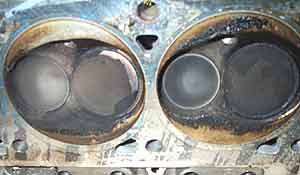
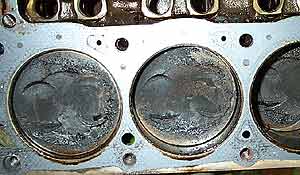
Poor valve train geometry on the Holley Systemax
heads led to the valve guides wearing out in just
10,000 miles. The result was oil consumption at
the rate of one quart per 200 miles. |
degrees.) The idea behind this
is to unshroud the intake valve, and thus increase airflow
into the cylinder. While the concept works, the problem
is the twisted valve changes the valve train geometry.
The result is the rocker arms place an increased side
load on the valve guides because of the reduced distance
between the centerline of the valve stem and the centerline
of the pedestal/stud mounting boss.
We discussed this problem at length with Brian Tooley
of Total Engine Airflow (coincidentally he was an engineer
at Holley, working on the Systemax project, before he
left to start his own company.) Brian told us that the
problem is made especially worse when customer mills the
Holley head, or installs it on a decked block, or uses
non-stock cam and rockers. All of these modifications
require properly checking the valve train geometry to
select the correct length pushrod. Brian also pointed
out that not all rocker arms are equal, even though they
may have the same ratio. His comparison of several different
brands of 1.6:1 rocker arms showed they all had different
overall lengths (between the centerline of the stud and
the roller tip.) This does not mean the rocker arm is
more or less than 1.6:1, but that the length of the arm
changes the sweep of the roller tip across the valve stem
as the valve opens and closes. This affects the amount
of load places on the valve guide, and thus it is critical
to measure using special valve train geometry tools. What
is interesting is that Holley does specify a longer than
stock pushrod when installing the Systemax heads on a
stock 5.0L engine. Unfortunately even this does not truly
correct the problem of accelerated guide wear.
Brian indicated that while it is standard practice to
check valve train geometry on a highly modified race engine,
it is not realistic to expect consumers to check it for
what is supposed to be a "bolt on" stock replacement
head. The only real fix for this problem is to re-design
the head so that the rocker mounting pad is moved in correlation
with the revised valve angles. Brian indicated that Trick
Flow had the exact same problem when it first released
the pedestal mount version of its Twisted Wedge Head.
Ultimately TFS discontinued the pedestal mount head and
now offers a stud-mount head with much improved geometry.
Needless to say, ten thousand miles after installing the
Systemax heads the motor was burning one quart of oil
every 200 miles! We had even converted the '88 to a T5
in this time span, in the hopes of knocking on the 12's
with our seemingly strong running combination. However
the one and only trip to the track with the Holley head
and T5 combo resulted in a 15.2 @ 100 - a dramatic example
of how much power is lost due to excessive oil consumption.
|
(Top
End Assembly.
|
|
|
|
|
|
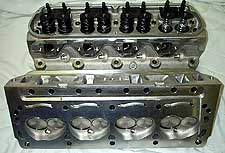
We selected the Edelbrock Performer
heads for this project. A tried and true head which flows
decent. |
|
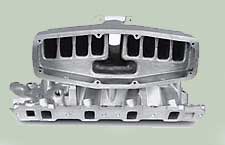
Staying with the Edelbrock package,
we opted for a RPM intake. This should match the rpm range
of the cam we select later in this article. |
|
|
|
Edelbrock
Head Flaw
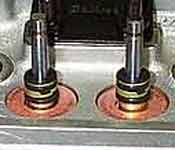
We
discovered that Edelbrock does not use valve spring cups on
these heads. In fact none of the Performer or Performer RPM
heads we looked at for small block Fords or even the FE heads,
had spring cups or even hardened shims! |
|
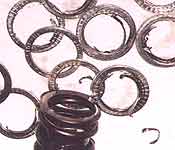
We
found this to be a huge oversight on Edelbrocks part. The
tool steel springs and inner damper will eventually tear up
the soft shims and spread shrapnel through out the motor.
Furthermore with soft aluminum you want to support and locate
the spring with a steel cup. |
|
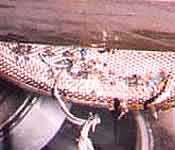 |
|