
Preventing Detonation
We knew going into this project that putting boost on
a 10.5:1 compression engine is an easy recipe for a blown
head gasket, or worse yet a damaged motor. We had to take
the proper precautions to prevent detonation and a lean
condition. This meant ensuring adequate fuel delivery
and quality, as well as controlling timing. We tackled
both of these before pushing the motor hard on the dyno.
In naturally aspirated form we ran the 331 with 14 degrees
initial and about 36° total (22° from the centrifugal
advance mechanism.) For boost we dialed back initial to
just 10°. However this yielded a total of 32°
and we wanted to start tuning with no more than 24°.
We adjusted the advance slot in the MSD Pro-Billet distributor
by increasing the diameter of the stop bushing, however
we could not get below 30° total. We called MSD for
some advice. They turned us to their Boost Timing Master
ignition system (see side bar.) The 6BTM will take out
1, 2 or 3 degrees of timing per psi of boost, up to 15
degrees maximum. If the Vortech S-trim puts out 6 psi
we should see 6, 12, or 15 degrees reduced from total
advance. In our case, with total at 32°, we can get
timing to a conservative 20 degrees.
The next step in preventing detonation would be to raise
the octane level of the fuel. The high static compression
combined with the high dynamic compression
and temperature increase from the boost pressure is likely
to result in spontaneous combustion due to pre-ignition
or detonation. If combustion occurs when the piston is
not in the top dead center position severe engine damage
will result. With 91 octane in the tank we were detecting
detonation at just mid-throttle in 4th gear. This was
a sure sign we'd be in for trouble at wide open throttle
on the chassis dyno. As a result we dropped in a few gallons
of 110 leaded race gasoline. Blended with the remaining
91 in the tank we figure we were at around 105 octane.
Boosted Dyno Results
We headed back up to Advanced Dyno and paid for their
ten pull tuning session, again using a wide-band oxygen
sensor to monitor air-fuel ratio. We anticipated that
proper tuning would take more than a day and planned to
make several runs today to check over the basics such
as proper fuel pressure, maximum boost pressure, and to
baseline the air-fuel curve. We made the first pull with
76/79 jets in the same 750 double pumper we'd been running
naturally aspirated.
The
air-fuel ratio on the first curve started
going dangerously lean almost immediately. At 5000 rpm
the curve went into the 16's (green plot below), and the
dyno operator frantically motioned the kill engine sign.
It was no surprise that horsepower was even less than
in naturally-aspirated form. A lack of fuel at best will
rob power, and at worst will rob you of an engine. Of
lesser concern but nonetheless eyebrow raising, was our
maximum boost was registering at only 4 psi on the playback
gauge. This may not have been a bad thing considering
any more boost would have increased the chance of engine
damage due to the lean condition.
The question was why was the carburetor was going so lean.
The dyno gurus again seemed to have an answer. They suspected
the power valve channel restriction (PVCR) was not able
to supply the amount of fuel the engine needed. Power
valves are generally in the
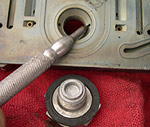
Power Valve Channel Restriction
(PVCR) diameter may have limited our engine performance. |
primary metering block and rated
to open at specific engine vacuum levels. This enables
a smaller jet size for fuel-efficient part throttle driving,
while enabling enrichment under high-load and wide open
throttle conditions. The orifice size of the jet plus
the orifice size of the PVCR determines the amount of
total fuel which can enter the primary circuit. In a blow-through
application the diameter of the PVCR often needs to be
increased to flow more fuel. As a temporary measure, and
test of theory, we removed the power valve and placed
a power valve plug in its place. We jetted up to 80's
in the primary and 84's in the secondary to compensate
for the fuel we would not be getting via the PVCR. This
is a common tactic for race cars but results in poor part
throttle fuel economy and performance for street cars.
The engine responded to the additional fuel and while
still dangerously lean at 14:1, power was up to 416 horsepower
and 410 lb.ft. of torque.
Dynojet
Results: Supercharged, 331cid
|
Peak Horsepower |
Peak Torque
(lb.ft) |
Initial |
351.1 @ 6000rpm |
400.2 @ 4000rpm |
Best |
424.6 @ 6000rpm |
406.4 @ 5100rpm |
|
|
Last Pull
With all systems checking out ok and no detonation detected
we jetted up the secondaries to 91 in attempts to get
the air-fuel ratio into the rich side. The third pull
continued the trend of increasing power while AF ratio
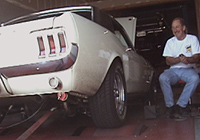
Advanced Dyno's H.H.Bennet
sports the usual mile wide smile after seeing the
power numbers resulting from his tuning advice. |
was
now at a steady 13.5 - still lean but getting closer.
We expected to see a much larger
change in AF ratio with the seven-size increase in secondary
jets. The fact that we
saw only a net change of 0.5 was an indicator that the
carburetor was at its' limits for supporting this engine.
This is not to say that the 750 cfm rating is the limiting
factor, but rather the carbs ability to meter the proper
amount of fuel for the amount of air being consumed by
the supercharged engine. This
didn't come as a surprise and in fact prior to this dyno
session we were already in discussions with a leading
carb tuner for a blowthrough specific carburetor.
The red plot in the chart above shows the third and final
pull for the day, with peak horsepower at 424 and torque
at 406 lb.ft. We
still are seeing only 4 psi of boost on the guage. The
S-trim blower is rated to produce between 6-8 psi on a
302 displacement engine. While 4 psi seems low it may
be due to the increased displacement of our stroker plus
the efficiency of the engine. The bottom line is not boost
but power numbers. Currently we're only netting 55 horsepower
and 65 lb.ft of torque above our naturally aspirated results,
but we're nowhere near being tuned. Watch for our final
article in this series with results from round two.
|
|
|
|
|
|
|
Turn
Back Time
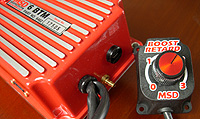
We're using MSD's Boost Timing Master
(6BTM) to retard timing as boost pressure builds.
A dash mounted dial enables 0-3 degrees of retard
per psi of boost. This will enable us to run
10-12 degrees initial and as little as 26 total
to ward off detonation.
The 6BTM box is
identical to the famed 6AL ignition, save for
the 1/8" vacuum nipple for boost reference.
Installation is equally as easy with the added
step of locating the timing dial within drivers
reach. |
Source:
MSD Ignition
Autotronic Controls Corporation
12120 Esther Lama, Suite 114
El Paso, Texas 79936
www.msdigniton.com
|
|
|
|
|