Dyno Time
With the heads installed on our 88k mile '93 Cobra we
were ready to rock n' roll. We headed up to Advanced Dyno
Technologies in Suisun, Ca, our local chassis dyno operator.
Shop owner 'H.H.' strapped the car down and installed
the wide-band air-fuel sensor which would allow us to
do some tuning. As the engine cooled from the drive up,
we chatted a bit about what we expected the car to put
down. I told him, cautiously, that if I made 270 peak
horsepower and over 300 ft-lbs. I'd be content.
Figure
1. Dyno Results 1993 5.0L Cobra engine, AFR 165cc heads,
ported Cobra lower intake. Red line is baseline pull, blue line
is final pull.
Pull
1
The first pull was made in "as is" condition
to obtain a baseline. The only difference between how
the car would be run on the street and these dyno pulls
was that we used an ice bag to allow the intake to cool
rapidly between runs. The initial pull was with 42lbs.
fuel pressure and timing at 13 degrees initial advance.
The results immediately settled my nerves - 293 horsepower
and 328 ft-lbs. of torque. Perhaps even more exciting
was the air-fuel (A/F) ratio at a
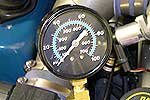
Adjusting fuel pressure was
a big factor in getting over 300 HP. |
fat 11.5:1. It was clear that the motor still had considerable
power to give once the A/F was leaned out.
Pull
2
Using the adjustable fuel-pressure regulator we backed
off pressure by 2 to 40lbs. After allowing the engine
to cool for 15 minutes we made another pull. (Each pull
is being made in 4th gear 1:1 gearing ratio from approximately
2500rpm to 6000rpm.)
As anticipated the car picked up power across the entire
curve due to the slightly leaner A/F ratio. In fact
the 1lb drop in fuel pressure barely registered on the
chart, showing A/F still in the mid 11:1 range.
Pull
3
For the finale in our three-pull session we continued
to work on getting the air fuel curve closer to the
stoichiometric ideal of 14.7 parts air to 1 part fuel.
While in chemistry this is the perfect burn, in a real
engine it is a little to lean and can result in detonation
if factors such as colder air or lack of fuel were to
occur. Most naturally aspirated gasoline engines run
best at around an A/F of 13.1.
We pulled out another 1lb of fuel pressure for the last
run. We would like to have pulled out slightly more,
however we were concerned by the dangerously lean A/F
ratio of over 18:1 (the large peak in the A/F curve)
before 3400 rpm. This actually was an indicator that
the vehicles O2 sensors needed replacement. The O2 sensors
are only used by the engines computer during part throttle,
at wide-open throttle the engine is strictly using the
mass air meter and look up tables within the computer
memory. So while the bad O2 sensors were not hurting
our dyno numbers, they were causing detonation during
the transition from part to wide-open throttle. Any
detonation is something to be worried about, so we played
it safe with just a 1lb drop in fuel pressure for the
final run.
This time the chart responded with a A/F ratio slightly
over 12:1. Still a little rich, but power improved remarkably,
to a best of 303 horsepower and a stunning 341 ft-lbs
of torque!
Conclusion
There was a time when making 1 horsepower to 1 cubic
inch was a big deal - and that was at the flywheel!
Today achieving those numbers at the rear wheels is
a testament to the advances in engineering and technology
of the aftermarket. What is even more impressive is
that this stout little 5.0L motor is in a fully-comfortable,
no hassle to drive, daily commuter Mustang. The idle
and driveablity are like-stock, and the power band is
all in a very usable, stoplight to stoplight rpm range.Look
for an upcoming article on track results from our new
project car. 
|