So
you're driving along and suddenly you feel a vibration coming
through the steering wheel. Or perhaps you're feeling it coming
through the floorboards and under your seat. Maybe you don't
really feel it all, but you hear it. The only thing worse than
driving a car with a vibration, is trying to find where the
bad vibes are coming from. Everybody eventually comes across
this problem, and rarely if ever is the problem found through
simple diagnosis. In a commuter car the problem is simply annoying
to the driver and passengers. In a built up street/strip car,
the bad vibe can be an indication of a component about to fail.
In both cases if the vibe is not discovered and taken care of,
there could result serious damage to the engine or drive train.
Having
been through our fair share of hair pulling episodes trying
to isolate shakes and rattles, we decided a "how to"
diagnosis article would be useful for our readers. Of course
not all of you are experiencing this problem right now, so skim
through this page and bookmark it. After all it is articles
like these that really prove to be a invaluable resource when
trouble strikes.
Vibrations
can be separated into there categories; engine related, driveline
related, and none of the above. Engine related vibrations are
typically caused by problems with the balance of the internal
rotating assembly, however they can also be due to other mechanical
or electrical factors affecting the engine. To isolate whether
the vibe is engine related, the simplest test is to place the
transmission in neutral and with the car not moving; check to
see if the vibration can be felt at idle, as well as throughout
the rpm range. If there is no vibration present, you know that
your problem is not related to the engine. If you do feel a
vibration, it is most likely engine related.
Driveline vibrations are generally caused by anything from the
transmission to the axle assembly, and the driveshaft in between.
Driveline vibrations can
only be felt when the car or rear wheels are in
motion. Typically if the vibration occurs in a specific rpm
range, it is driveline related. If it occurs at a specific speed,
suspect the wheels.
Finally there are types of vibrations that don't fall into any
of those categories; in fact they can be
vibrations due to normal engine harmonics.
Once you've determined the general category of the vibration,
the next step is to systematically go through the usual trouble
areas as listed below.
External
engine: Worn or separated motor or transmission mounts can
lead to some funky vibrations. Broken mounts are hard to detect
without getting under up close and really inspecting the rubber
section of the mounts. Also check the rubber layer sandwiched
in the harmonic balancer. Many times the rubber will separate
allowing the outer section of the damper, which contains the
counter weight, to move and change the engine balance.
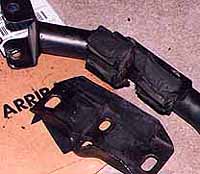 |
 |
Take
a very close look at transmission and motor mounts.
The rubber can separate, but with the weight of the
engine or transmission compressing the mount, you'd
never detect it at a glance.
|
Internal
Engine: This category primarily deals with engine balance.
If you just built up a new motor, or bought
a used one, and it has had a vibration from the minute you first
fired it up, chances are the problem is in the balancing of
the engine. Ford engines have used a variety of balance factors
over the years. All small block Fords, including the 351C and
400M are externally balanced. However the early 221-302's
used a 28oz. counterweight factor while recent years all use
a 50oz. imbalance. This means you
must use the same crank, harmonic balancer and flywheel or flexplate.
The Ford FE's, 429 and 460 engines are all internally balanced,
except, for the 410 and 428. Also the Ford truck series (FT)
are all externally balanced, so keep this in mind if you are
using the heavy duty forged steel cranks from the FT in your
FE buildups. Using mismatched harmonic balancers, cranks, or
flywheels is guaranteed to cause vibration problems. There is
no two ways about it, it will occur, and it will be very noticeable.
As a matter of fact, it will result in destroyed bearings in
short order.
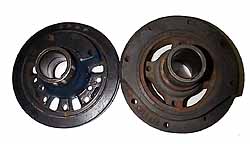 |
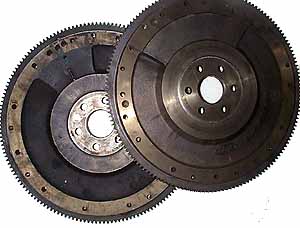 |
Small
block Ford harmonic balancers and flywheels used 28oz
counterweights in the early years then switched to 50oz.
Mixing the two varieties will cause serious engine balance
problems. |
However
just because you use the correctly matched crank, balancer and
flywheel, does not ensure a smooth spinning engine. New pistons,
rods and even clutch pressure plates also effect the balance.
Thus it is a good idea to always include a balance job when
building or rebuilding an engine. Most good machine shops can
take mismatched crank, flywheel and balancer and adjust them
to achieve the proper balance. This means that if you need to
use a four bolt 50oz damper on your 289, your machinist can
make the proper weight adjustments to make this possible.
Most Ford flywheels/flexplates are indexed to the crank; meaning
they only bolt on one way in order to properly phase the counterweights.
While it may look like the mounting holes in the flywheel are
evenly spaced, they are not. Many times inexperienced individuals,
thinking their flywheel was drilled incorrectly, try to solve
the problem by enlarging or egging out the holes. This will
result in the counterweights being in the wrong position, and
a horrendous vibration. If you've bought a used engine or flywheel,
and can't find the cause of a vibration, check this out.
Ring gear separation. This is rare, but it has happened to us.
The tack welds holding the ring gear to the flywheel came apart.
This in itself may not cause a vibration, but in our case it
led to improper phasing of the clutch pressure plate. Good machine
shops ask for the clutch pressure plate, so they can balance
it along with the rest of the rotating assembly. They usually
stamp an indexing mark on the ring gear and the pressure plate
so you can line them up properly. In our case, since the ring
gear had come loose, the index mark had moved, so when we bolted
up the pressure plate it was actually in the wrong position.
It took five weeks and as many tranny removal/installs to find
this vibration!
Torque convertors are also neutrally balanced. While it is very
rare for a torque convertor to cause an out of balance, a convertor
that has separated or the internals have come apart can certainly
create a vibration or rattle. Usually this is accompanied with
a poor performing and slipping transmission.
Misfire
A very common cause of vibrations is a misfiring cylinder. Of
course you'll be able to tell this apart from a mechanical problem
due to the performance loss, but nevertheless it can and has
been overlooked. A cracked spark plug insulator, smashed gap
or broken ground strap, are some of the causes. If you suspect
a misfiring cylinder, the best was to isolate it is to pull
each spark plug wire one by one, at idle, and notice the resulting
rpm drop. A misfiring cylinder will not result in an rpm drop.
Transmission: There is not much within a transmission
itself, manual or automatic, that will cause a vibration without
any other symptoms, such as poor shifting or slipping. However,
as mentioned above, a pressure plate that is out of balance
can cause a vibration. Pressure plates are supposed to be neutrally
balanced from the manufacturer, but they rarely are exactly
zero. If you experience a vibration after installing a new clutch,
the pressure plate could be the problem. Have it matched balanced
to the old one.
Other transmission areas to check:
Loose or misaligned bellhousing.
Worn or missing pilot bushing/bearing.
Worn tailshaft bushing.
Driveshaft,
Rearend gears, and pinion angles: Driveshafts also need
to be balanced. However if the driveshaft is damaged, or bent,
it wont spin true and result in a vibration. Most factory driveshafts
are "phased" with the rear pinion yoke. Usually there
is yellow or other colored paint marks on the driveshaft and
pinion yoke to designate the phasing. If you've had the driveshaft
out recently, try reinstalling it 180 deg. over and see if it
clears up the vibration. Worn u-joints will certainly cause
a vibration and "clunking" upon braking or acceleration.
Check them periodically.
While rearend gear problems don't typically manifest themselves
in a vibration, gear ratio changes do contribute to certain
types of driveline vibrations. Actually the vibrations are a
result of the change in speed of the driveshaft as a result
of a gear ratio change. The length, diameter, composition, and
angle of a driveshaft, as well as the final gear ratio, determine
what rpm (technically called the "half critical" speed)
at which the driveshaft will experience a natural vibration.
(Incidentally, critical speed, is a physical term for the speed
at which a rotating shaft begins to wobble and become unstable
As you can imagine, this can be a very dangerous condition for
a driveshaft. Fortunately for most driveshafts, this does not
occur until well over 10,000 rpm.) All driveshafts have a certain
level of vibration, but with the typical factory gear ratios
of 3.27 and lower, the vibration may not occur until above 5000
engine rpm - well beyond the typical sustained driving rpm.
Numerically higher gear ratios will bring this range lower.
So if you install a set of 4.56 gears and suddenly feel a vibration
while cruising on the freeway at 3000 rpm, it is most certainly
due to the gearset lowering the the half-critcial speed of the
driveshaft. Aluminum driveshafts do a better job at dampening
vibrations than their steel counterparts. If you've isolated
a particular vibration as being due to a gear ratio change,
an aluminum driveshaft may help out.
Excessively lowered (or raised) vehicles are prone to driveline
vibrations due to the severe angles placed on the driveshaft
and u-joints. The ideal angle of the driveshaft should be between
0 and 3 degrees sloping downwards from the transmission to the
rearend. To measure the driveline angle, use a degree finder
to measure the angle of the driveshaft (wheels must be on the
ground or loaded on a lift.) Then measure the angles of the
front slip yoke, and the rear pinion yoke and determine the
average of the two. Subtract the driveshaft angle from the average
of the two yokes and that is the static operating angle of the
driveshaft. If you suspect a driveshaft angle problem as the
cause of the vibration, find a good driveline shop that can
help you properly setup the correct geometry.
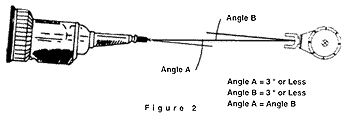 |
Improper
driveshaft angles can result in vibrations and accelerated
u-joint wear. For engines operating at 5000+ rpm, the
driveshaft should not be at more than a 3 degree angle.
[Image from http://www.iedls.com/guide.html
] |
If
you can't pinpoint the vibration in the engine or drivetrain,
start looking elsewhere. Listed below are some other elusive,
but common, causes of vibrations.
Wheels
and Tires: Everyone has at one point or another experienced
an out of balance wheel. The vibration is occurs at a very specific
vehicle speed, rather than engine rpm, and can be felt in the
steering wheel or the seat. The easiest way to isolate an out
of balance wheel is to rotate the suspect wheel and see if the
location of the vibration changes. If you feel it in the steering
wheel, move the front wheels to the back, and see if it is now
felt in in the seat or under your feet. Of course if you just
got a new set of tires and neglected to balance the wheels,
you may get a vibration from all four wheels. If the vibration
appears out of the blue, check the wheels to make sure a balancing
weight did not fall of.
Other
areas to check:
- Wheels out of alignment.
- Flat spot on tire or radial belt separation.
- Exhaust pipes or header tubes touching the chassis or interfering
with steering components.
- Broken or wobbling cooling fan.
- Worn waterpump, alternator, or AC compressor bearings.
- Worn axle
bearings.
- Warped brake rotors or drums.
- Excessive play in ball joints, tie rods, steering box/linkage.
- Loose body panels or window glass.
- Excessive electric fuel pump noise.
|